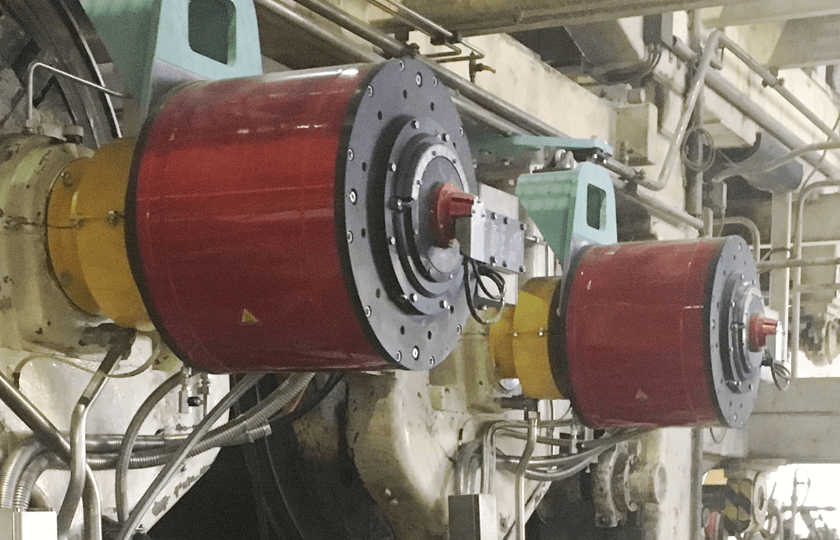
04 Jun 2019 Rebuild of the BM 3 to the latest motor technology from AS Drives & Services GmbH
Rebuild of the BM 3 to the latest motor technology from AS Drives & Services GmbH
At the Annweiler site, the Kartonfabrik Buchmann GmbH produces on the Board machine 3 (BM 3) raw board for the production of folding boxes with a grammage of 230-500 g/m². The BM 3 has a working width of 4.400 mm. In January 2019 the BM 3 started with a new drive technology.
The drive of the BM 3 before the rebuild
The BM3 dryer groups were driven by a large number of different gear-based drive systems.
Some of them where closed wheel housings with Voith TEK gearboxes, some where various shaft-mounted gearboxes and some special solutions with direct motors that are directly connected to the closed wheel housing. Most of the drying cylinders of a group were form-fit connected to each other via gear units. A dryer-cylinder-drive via the dryer fabric was not realized before the rebuild yet. After a while, this was followed by tensions which became apparent in the form of increased wear and friction losses on the gear technology. As the machine running time increased, the diameters of the cylinders changed as a result of scraping interventions. This resulted in speed deviations, which the existing drive system could not compensate in the long term.
The old electric drive consisted of standard asynchronous motors, which were placed on steel platforms outside the machine hood. In addition, pre-gear units were necessary to achieve the required torque. The total drive thus consisted of a chain of wear parts, e.g. closed wheel housing, Voith TEK gearboxes, pre gearboxes, couplings, cardan shafts. This large number of drive elements led not least to a large stock of spare parts.
(Abb. 1, 2, 3).
Reasons for the rebuild
One of the main reasons for the rebuild of the drive of the BM 3 was to increase the speed from 400 m/min to 800 m/min (constructive). The first step was to equip the drive of the dryer section of the KM 3 with a modern drive technology. The desired speed is then only limited by the press- and wire sections.
Another important reason for the drive modernization was the large number of obsolete drive types and the related problems. In particular, the closed wheel housing often tended to leakages, causing oil to come out uncontrolled. The enormously high and thus cost-intensive stocking of spare parts for the various drive types was another reason for the modernization.
After all, the old drive systems led to tension in the drive, to sheet flutter and to damages at the gearboxes and the couplings.
The new drive
In its search for a new, compact and powerful drive system, the Kartonfabrik Buchmann GmbH chose the FlexoDirect® motor solution from AS Drives & Services GmbH (Reken). This synchronous motor is mounted on the cylinder journal and drives the cylinder directly. All intermediate gears, drive shafts or pre-gearboxes could thus be omitted.
Buchmann decided to install the motors on the tending side.
In order to mount the motor on the dryer cylinders, AS Drives replaced the cylinder journal on the corresponding cylinders, which should be driven. All torques occurring during operation are absorbed by a flexible torque support. This is designed in such a way, as to prevent the torque support from becoming distorted and tearing off. Due to the compact size of the motor, the FlexoDirect® can be installed inside the hood. A breakthrough through the dryer-hood and the associated heat losses are thus avoided.
In this project, a total of 29 drive cylinders were determined and equipped with the FlexoDirect® FZ05. These motors drive the entire dry section of the BM 3. The dryer felt drives the cylinder, which are not equipped with a FlexoDirect®. This prevents the cylinders from being distorted by the drive system.
The FlexoDirect® series have been selected in the way that only two different types are required to cover the required performance spectrum. The power density of the installed FlexoDirect® is between 3.000 – 4.000 Nm.
Also, only one spare motor per series is required as a spare part requirement. This is an enormous improvement compared to the warehousing of the old drive system.
Parallel to the installation of the new direct drive, all old drive systems were uninstalled. The steam heads could be reinstalled on the drive side without any major modifications. Only the old closed wheel housings were modified by AS Drives in such a way that the oil flow no longer flows through the entire wheel housing, but is only directed to the cylinder bearings, from where it flows directly back to the central oil lubrication system. Thus the oil leakages at the wheel housing were eliminated. The wheel housing itself remains as the supporting element of the machine frame.
Due to the installation of the motors inside the drying hood and the temperatures there, AS supplied an appropriate cooling unit (Cooliflex®) to temper the motors with cooling water. The flow controllers FlexoFlow® Water are used to maintain the optimum temperature in the motors at all times. These supply the motors with an appropriate cooling water flow depending on the motor temperature, which is permanently monitored, and so the motors always are kept at the optimum temperature. In this way, the motors are cooled during operation and kept at the right temperature during standstill to prevent them from falling below the dew point. One flow controller monitors and supplies two motors with corresponding cooling water.
The new lubrication technology
In addition to the drive technology, AS Drives also modernized the existing lubrication technology. The old central lubrication system did not have any degassing function in the tank to free the returning oil from harmful air bubbles. These air bubbles occur during operation (when the oil passes the gearboxes, bearings and wheel housing) and have an enormous effect on the lubrication performance. The new Lubriflex® lubrication system from AS Drives processes the oil in such a way that it can be returned to the lubrication points almost 100% free of air bubbles. An appropriate degassing unit in the tank of the Lubriflex® makes this possible.
In addition, before the rebuild, the oil flow was only monitored by simple flow meter. Changes to the oil flow had to be adjusted manually. The leaks in the wheel housing and in the pipelines repeatedly led to oil losses in the system. AS Drives installed the intelligent flow controllers FlexoFlow® as a part of the modernization. These flow controllers not only monitor the oil flow, but also control it fully automatically. For this purpose, the current flow rates are permanently measured and compared with the set values. If deviations occur, a servomotor on the FlexoFlow® immediately readjusts the flow via a control throttle.
All old pipes were replaced in the course of modernization to prevent leakages. AS Drives and its installation team took over the complete piping of all lubrication points and the integration of the new lubrication system.
Comment by project manager Armin Lehmann (Head of Technology at Kartonfabrik Buchmann GmbH)
We are very satisfied with the installation of the new drive technology. The entire rebuild worked smoothly and we were able to resume production after 13 days of rebuild thanks to the good preparatory work of all the companies involved and the good project management.
The synchronization problems caused by the various drive systems at that time have now been completely eliminated. We also have a much better control of the sheet flutter with the new direct drive.
The colleagues from the production and the technology, with the support of the suppliers, quickly succeeded in working out the optimal adjustment and eliminating minor errors.
The fears that our papermakers might have problems with the tending-side assembly of the motors during paper production did not come true. The head height is still absolutely sufficient and our employees can easily move along the machine.
We are also very pleased with the spare parts situation. Handling the various types of drive was not always easy. With the new drive solution, we only need two spare motors and that is an enormous improvement for us. The new flow controllers are also an improvement.
In the future, we also plan to rebuild the guide rolls and the wire and press sections in order to achieve the desired speed of 800 m/min.